News
Creating Coatings for Extreme Environments: From Solar Shields to Hypersonic Leading Edges
Researchers at the Johns Hopkins Applied Physics Laboratory (APL) in Laurel, Maryland, are developing coatings that can stand up to the rigors of hypersonic flight in the upper atmosphere. The work — building on decades of experience with hypersonics systems and the development of a custom heat shield coating for the thermal protection system (TPS) on NASA’s Parker Solar Probe — leverages APL’s ability to produce custom materials solutions to solve hard problems that stand between success and failure on real missions.
Hypersonic vehicles operating in the upper atmosphere are subject to speeds exceeding Mach 5 (five times the speed of sound) as well as temperatures well over 1,000 degrees Celsius, oxidation from the atmosphere and tremendous aerodynamic shear loads. The leading edge (or nose) of these vehicles needs to be protected against these conditions, as do fins, control surfaces and apertures.
“We can’t just take Parker Solar Probe’s heat shield coating and apply it to a hypersonic vehicle, because space is an airless environment,” said Keith Caruso, a materials expert who was a key contributor to the Parker Solar Probe coating and is now involved in the Lab’s hypersonics coatings efforts. “But the upper atmosphere is not airless, so hypersonics vehicles have to deal with a very specific and demanding set of pressures that space vehicles don’t face,” he added.
“Materials should be core to the design process from the very beginning, in order to ensure system survivability,” said Morgan Trexler, who leads APL’s Science of Extreme and Multifunctional Materials program. “If we understand the envisioned mission and environment, we can create enabling custom materials. But to be successful, this takes time and customized materials innovation, in close coordination with system development.”
The heat shield coating for Parker Solar Probe needed to be able to withstand the tremendous heat of the Sun, while also deflecting its light as much as possible. It had to be applied to a carbon substrate without chemically reacting, while maintaining its structural integrity and resisting changes in volume as well as in color. There were no existing coatings that could meet these unforgiving requirements, so APL scientists created one from scratch, layering three different ceramic oxides, as well as metals, in a variety of configurations and testing them until they produced a coating that was up to the challenge.
Since its launch in 2018, Parker Solar Probe has completed 10 close approaches to the Sun, coming within about 6.5 million miles of the Sun’s surface while moving faster than 330,000 miles per hour — all while keeping the spacecraft’s instruments at roughly room temperature — demonstrating the success of APL’s TPS. The probe also made history as the first spacecraft ever to touch the Sun. Since developing the TPS, the Lab has taken the lessons learned, and capabilities developed, and applied them to the challenge of developing coatings for the hypersonic environment.
It’s a challenge that APL is well equipped to meet. Since 2015, the Lab has been strategically investing internal funding in the development of coatings for the hypersonic environment. The investment, as well as an ongoing partnership with the Office of Naval Research, has yielded capabilities and frameworks that allow the Lab to take coatings development to a level well beyond what was required to produce those for the Parker Solar Probe TPS.
“When we developed the Parker Solar Probe coating, our capabilities were at a very early stage comparatively,” Caruso said. “It involved a lot of trial and error, but we now have systems and processes in place to systematically produce and evaluate new coatings at scale and in the context of specific mission requirements.”
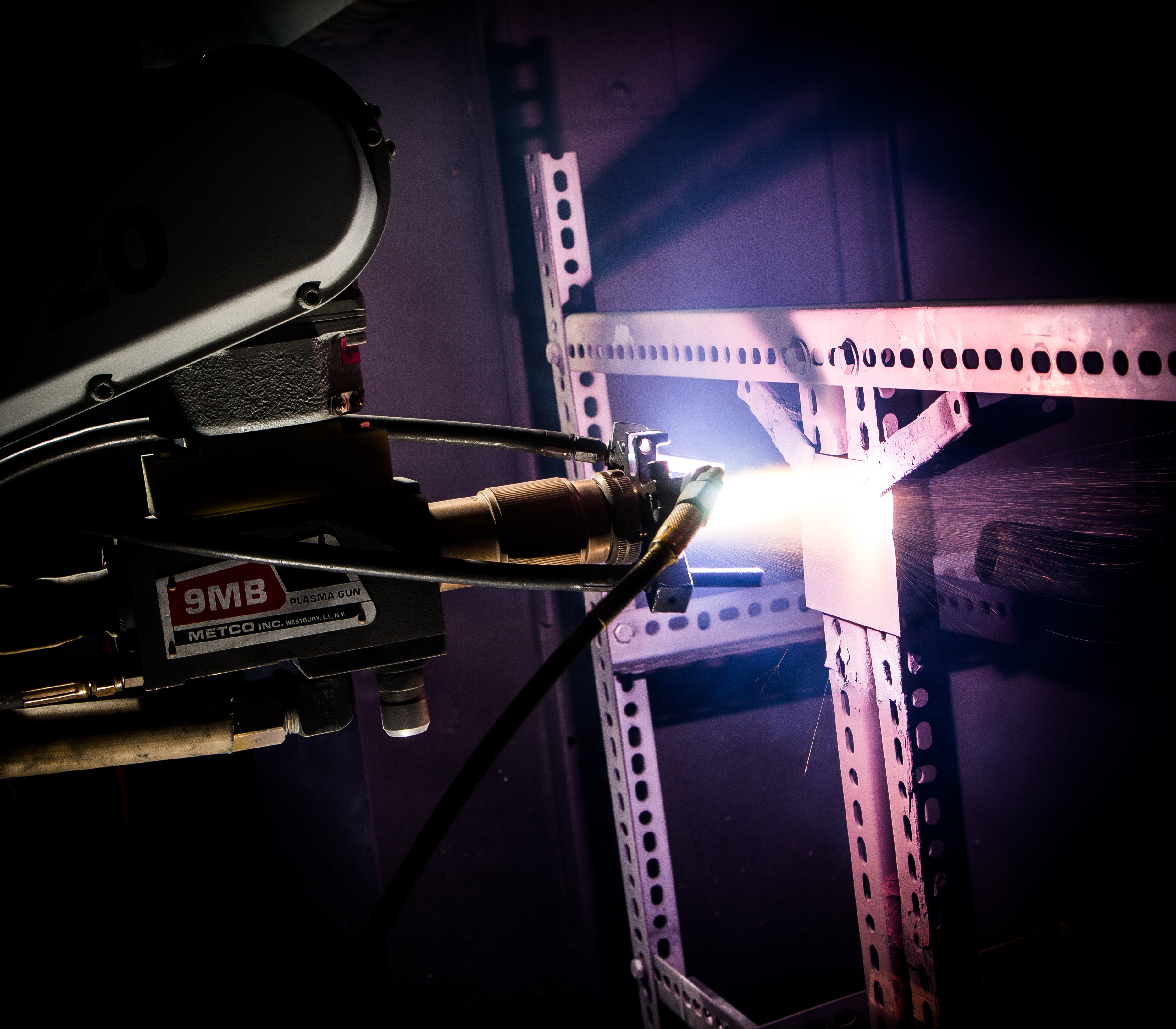
Credit: Johns Hopkins APL
On the capabilities side, APL has developed a state-of-the-art thermal spray facility able to apply a wide range of liquid solutions, liquid suspensions and solid particulates, such as refractory ceramics. A high-velocity oxygen fuel torch enables rapid testing of tens of samples per day under Mach 2-3 and temperatures exceeding 2,000 degrees Celsius, with the ability to simulate the thermal profiles of flight trajectories of interest. The Lab has also developed a modeling and simulation framework in collaboration with the Materials Architectures and Characterization for Hypersonics (MACH) program at the Defense Advanced Research Projects Agency (DARPA), to evaluate materials survivability in the context of specific hypersonics mission requirements.
The latter capability highlights what sets APL apart as a trusted partner in the hypersonics domain, said Michael Brupbacher, a materials scientist at APL who is involved in the Lab’s hypersonics work.
And this coupled technical expertise and operational insight is highly valued by government sponsors focused on enabling future missions. “Johns Hopkins APL is…able to connect materials developments with platform performance,” said Bill Carter, the DARPA Defense Sciences Office program manager who leads the MACH program, under which the modeling framework was developed.
“The Lab has been working closely with the government and the defense industry for decades to develop hypersonics systems. Along with understanding the chemistry, we have a deep familiarity with the requirements and the practical realities of this environment,” Brupbacher said. “As a result, we’re able to generate unique insights that aren’t easily replicated elsewhere and that have a direct and tangible impact on the mission readiness of these systems.”
Caruso agreed, noting that APL’s technical capabilities are important but derive their true value from the unique blend of academic expertise and practical, applicable experience of the Lab’s researchers. Dating back to the 1940s, when the Lab began development of supersonic ramjet missiles, APL continues to contribute to the nation’s hypersonics effort in myriad areas.
“We have top-of-the-line plasma spray facilities, additive manufacturing capabilities and so on, but a lot of places have impressive equipment,” said Caruso. “Not a lot of places have the knowledge to do custom sol-gel processing — creating chemicals at the nanoscale, from the bottom up, so to speak. And still fewer places can do it with mission intent, with a view to hypersonics applications. There’s a real art to it, which APL has a firm grasp on and that other laboratories can’t reproduce.”
That knowledge is the result of APL’s history of hypersonics innovation, as well as an ongoing commitment to strategic hiring, said Dale Clemons, who leads the Multifunctional Materials and Nanostructures Group in APL’s Research and Exploratory Development Department, which helps guide the development of hypersonics coatings.
“Hypersonics is a very niche area to hire for — it requires an in-depth understanding of multiple disciplines to design materials for this environment and understand how they perform,” Clemons said. “For decades, we’ve been a recognized leader in materials development and testing in hypersonics, so we’ve cultivated a wealth of relevant expertise over time. Finding and hiring the right people is ultimately what enables us to stay at the forefront of the field.”
APL has produced a number of coatings that show promise in protecting leading edges and apertures of hypersonics vehicles and meet the requirements for offensive and defensive missions, according to Coire Maranzano, a program area manager in the Precision Strike Mission Area in APL’s Force Projection Sector, and Jim Schuh, an assistant program area manager in the Integrated Warfare Systems Program Area in the Lab’s Air and Missile Defense Sector.
“We are working closely with the Lab’s materials researchers to develop, test, implement and transition advanced materials into programs of record for a variety of offensive missions,” said Maranzano.
Schuh concurred: “The Lab’s coatings work is enabling defensive capabilities that will help the United States maintain the decisive advantage in the hypersonics domain.”
The Lab has gleaned insights from its recent hypersonics work that will continue to inform further development of materials in this and other extreme environments — whether in space, the upper atmosphere or any other environment inhospitable to matter. Key among these insights is the centrality of materials design to viable hypersonics systems.
“APL is well positioned to extend the life span of existing hypersonics systems,” said Trexler, “and to enable even more functional and resilient systems in the future.”